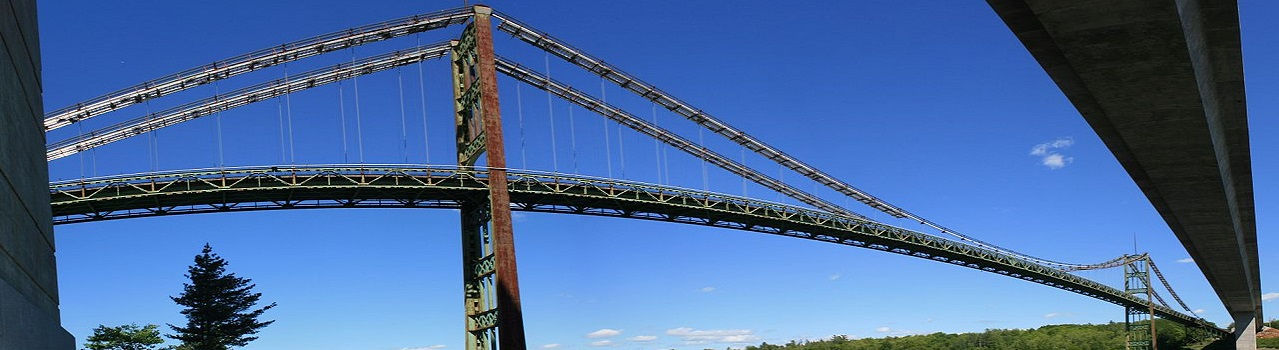
Laser scanning provides the ability to capture data even in low light conditions. Even within the poorly lit areas of Ballast Tanks, the scanner operates effortlessly, providing a 'night vision' perspective of the site. The operation gathers millions of data points, resulting in a comprehensive point cloud of the project. This abundance of data offers the design team ample information for the retrofit of the Ballast Water Treatment System (BWTS).
During the design and construction stages of a ship, water ballast tanks are strategically placed at various locations to ensure the ship's stability and trim during sea voyages.
As ships continue to increase in size and the cargo carried by vessels varies from one port to another due to global economic factors, the condition of the ship, and local voyage requirements, water ballast tanks play a crucial role in maintaining the trim and stability of the vessel for a safe sea passage. These tanks are essential for compensating and adjusting the ship's weight distribution, ensuring optimal stability and maneuverability throughout the journey.
Ballast water tanks laser scanning
Enclosed spaces constitute a fundamental element of the ship's structural design and are indirectly pivotal for the shipping company's economic efficiency.
A substantial portion of the ship's revenue, stemming from cargo (both dry and wet), is extracted from capacious hollow areas commonly referred to as 'tanks' within the ship's layout.
Notably, the steel tanks significantly contribute to the ship's stability, particularly when stability is influenced by the filling and discharge of fuel oil or ballast/domestic water. Given the immense importance of these compartments, regular maintenance is imperative.

Laser Scanning of Double botton Ballast Water tanks

Laser Scanning of botton and side Ballast Water tanks
Scheduled inspections and routine cleaning/repair activities are crucial to ensuring the optimal condition of the ship's hull and its constituents.
Laser scanning is viable even in complete darkness. This capability allows for measurements and visualization in areas with no illumination. In dark conditions, the scanner cannot capture colors unless supplemented with artificial lighting, yet the resulting point cloud imagery closely resembles night vision. Previously obscured details become prominently visible in the 3D model.
Locations of Ballast Tanks on ships
The water ballast tanks are provided at different locations depending upon the type of the ship. Following are some of the most common locations for construction of ballast tanks on ships:
Topside Tanks
The topside tanks, positioned at the topside corner of the ship and prevalent in bulk carrier ships, boast a distinctive triangular shape supplemented by wings on either side of the cargo holds. The construction of these tanks incorporates transverse frames organized in the following manner:
-
Deck Transverse: Situated beneath the main deck, providing support to the deck plating.
-
Bottom Transverse: Constitutes a crucial element of the supporting frame for the lower region of the topside tank.
-
Side Transverse: Contributes to the structural support for the side shell plating of the tank. It is aligned with the side shell frames within the cargo holds, particularly in single skin bulk carriers."
Double Bottom (DB) Tanks
The ship's double bottom serves as a crucial safety measure against water ingress in the event of grounding or collision. These void spaces also function as storage for ballast water, contributing to the ship's stability. Positioned between the forward part (up to the collision bulkhead) and the aft peak bulkhead, the double bottom tanks effectively divide the engine room.
In specific types of vessels like container and bulk ships, the double bottom space is subdivided transversely into three sections instead of the usual two. This division creates a cofferdam in the center, known as the duct keel, which houses valves, pipings, and equipment related to the ship's ballast and bunkering systems alongside carrying ballast and bunker tanks, enhancing operational efficiency and safety of the vessel.
Fore and Aft Peak Ballast Tanks
The fore and aft peak ballast tanks serve the specific purpose of precise trimming operations for the ship. These tanks are carefully filled to a partial level to achieve the required trim, minimizing the free surface effect of the liquid.
The construction of these tanks differs from the other ballast tanks on the ship due to their irregular shape, dictated by their location and their dependence on the bow and stern design of the vessel.
The design of these ship ballast tanks is characterized by a narrow bottom end, and as the tank ascends, the width expands significantly. The breadth of the tank corresponds to the breadth of the ship's hull, aligning with the overall design of the vessel.

3D Laser Scanning of side Ballast Water tanks

Laser Scanning of Ballast Tanks for BWTS retrofit
Wing Tanks
Located on the sides of the cargo holds, extending the breadth of the ship's hull. Commonly found in oil tankers and bulk carriers, they help stabilize the vessel by adjusting ballast levels.
Deep Tanks
Integrated into the deeper regions of the ship's hull, contributing to stability and providing additional ballast capacity for larger vessels.
Saddle Tanks
Tanks located near the sides of the ship, often shaped like a saddle, contributing to stability and weight distribution.
Inter-barrier Tanks
Positioned between the inner and outer hulls, enhancing safety and stability by preventing ingress of water in case of outer hull damage.
Ballast water presents a significant concern in the maritime industry due to its impact on oceanic ecosystems. Ships often take on fresh or seawater, known as ballast water, to stabilize the vessel during the voyage, adjusting for changes in cargo load. However, this practice poses an ecological problem. When the ship unloads its cargo and releases the ballast water at the destination, it may inadvertently introduce bacteria and small marine life from one ecosystem to another. This can disrupt the local ecosystem and potentially lead to an invasion of foreign species.
To mitigate this issue, shipping companies are incorporating treatment tanks into their ships to clean the ballast water before discharge, ensuring it doesn't introduce foreign marine life into the destination ecosystem.
During the installation of these treatment tanks, a 3D laser scan of the ship's engine room becomes a critical component of the workflow. As this tank is a new addition, it must integrate seamlessly into the existing network of pipes responsible for managing ballast water flow. This integration is a significant undertaking, and a 3D laser scanning provides highly detailed information essential for precise planning and execution of this complex project.